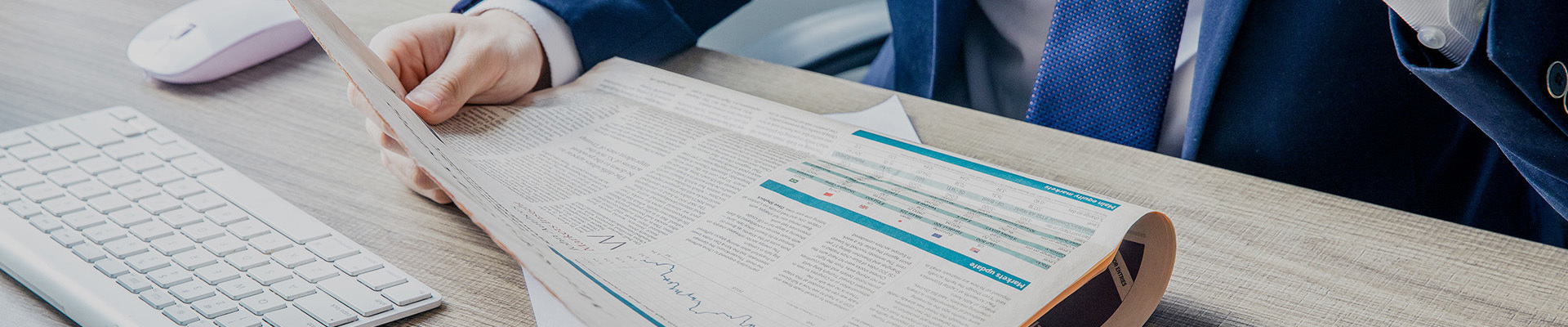
What are the methods for cleaning closed cooling towers?
2022-09-27 10:31
Because most of the cooling water contains calcium and magnesium ions and acidic carbonates. When cooling water flows over metal surfaces, there is carbonate production. In addition, the oxygen dissolved in the cooling water can also cause corrosion of the metal and the formation of rust. Due to the generation of rust scale, the heat transfer effect of the closed cooling tower is reduced. In severe cases the cooling water has to be sprayed outside the casing and the scaling can block the tubes in severe cases, rendering the heat exchange ineffective. The data from the study shows that scale deposits have a huge impact on heat transfer losses, causing increased energy costs as the deposits increase. Even a very thin layer of scale can increase the operating costs of the scaled part of the plant by more than 40%. Keeping the cooling channels free of mineral deposits can go a long way to improving efficiency, saving energy and extending the life of the equipment, while saving production time and money.
For a long time traditional cleaning methods such as mechanical methods (scraping, brushing), high-pressure water, chemical cleaning (acid cleaning), etc. in the cleaning of equipment, there are many problems: can not remove deposits such as scale, acid corrosion of equipment to form loopholes, residual acid on the material to produce secondary corrosion or corrosion under the scale, * eventually lead to the replacement of equipment, in addition, the cleaning waste liquid is toxic and requires a lot of money for wastewater treatment. In response to the above situation, domestic and foreign efforts to develop a small corrosive cleaning agent for metal, and the development of successful Fositech cleaning agent. It has high efficiency, environmental protection, safety, non-corrosive characteristics, not only good cleaning effect and no corrosion of equipment, can make the long-term use of closed cooling tower.
Closed cooling tower materials are generally based on carbon steel, stainless steel and copper, the carbon steel tube plate in the closed cooling tower as the use of its tube plate and tube welding seam often appear corrosion leakage, leakage into the cooling water system will cause pollution of the environment and waste of materials. Closed cooling tower in the production, tube plate and tube welding is generally used manual arc welding, welding seam shape there are different degrees of defects, such as depressions, porosity, slag, etc., the distribution of weld stress is not uniform. When using the tube plate part of the contact with industrial cooling water, and industrial cooling water impurities, salts, gases, micro-organisms will constitute the corrosion of the tube plate and weld seam. Research shows that industrial water, whether fresh or sea water, will have a variety of ions and dissolved oxygen, where the concentration of chloride ions and oxygen changes and plays an important role in the shape of corrosion of metals. In addition, the complexity of the metal structure will also affect the corrosion shape. For the closed cooling tower corrosion problems, the traditional method to fill welding, but fill welding easy to make the internal stress of the tube plate, it is difficult to eliminate, may cause the cooling tower tube plate welding seam again leakage. Now the western countries mostly use the method of polymer composite materials to protect the closed cooling tower cleaning and maintenance.
*** Translated with www.DeepL.com/Translator (free version) ***
Recommended
Landline
Address
No. 16, Baishijian Road, Langxi Industrial Park, Anhui Province
©2022 Anhui XILENG Environmental Protection Technology Co., Ltd Powered by www.300.cn Seo